Pellet Mill Roller in USA
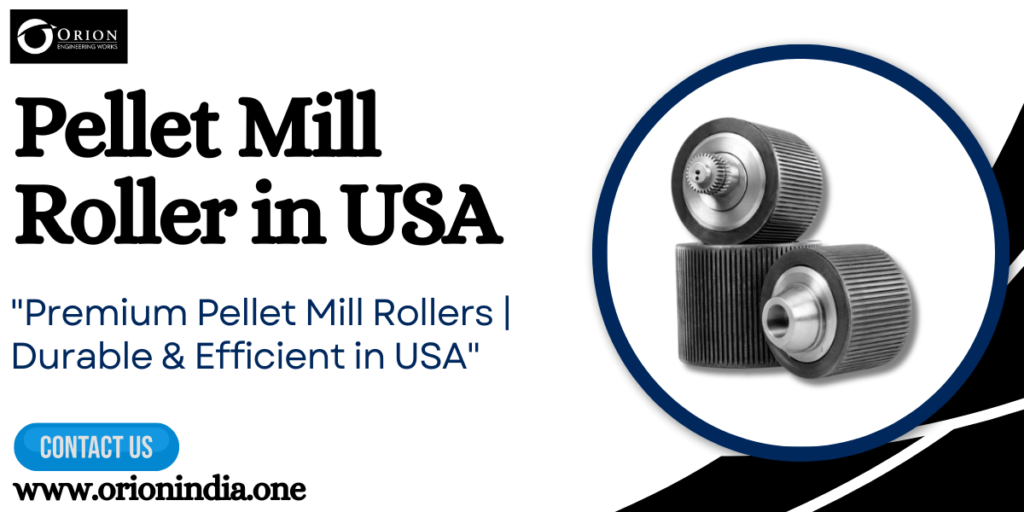
Table of Contents
Introduction
Welcome to Orion Engineering Works, a leading manufacturer based in the heart of India, (Punjab), Specializing in high-precision pellet dies, press rollers, elevator belts, and buckets. When it comes to pellet mill dies, we pride ourselves on being the best quality manufacturer in the industry. Orion Engineering Works is dedicated to delivering top-quality components for various industries. With a robust production capacity of over 2800 units annually, we cater to pelleting plants involved in animal feed, minerals, wood products, waste recycling, and beyond. We are the best Pellet Mill Roller Supplier.
The pellet mill roller is an essential part that quietly boosts productivity and efficiency in the busy world of American agriculture, animal feed manufacturing, and biomass energy. Despite being frequently disregarded, this small component is essential to turning raw materials into reliable, premium pellets. This article explores the purpose, kinds, maintenance, and crucial role that pellet mill rollers play in a variety of businesses in the United States.
What is a Pellet Mill Roller?
Compression is a straightforward but effective technique at the core of a pellet mill. Using pressure and friction, raw materials—such as wood shavings, animal feed, or agricultural waste—are pushed through a die. The dense, homogeneous pellets produced by this technique have many benefits for handling, storing, and using.The main part in charge of exerting this important pressure is the pellet mill roller. It functions in tandem with a die that has holes positioned appropriately. The material is forced through the perforations and forms pellets as the rollers rotate, pressing it up against the die’s inner surface. We are the best Pellet Mill Roller Manufacturer.
Why Choose Orion Engineering Works?
- Superior Quality and Durability: To create rollers that are long-lasting, Orion Engineering Works uses premium materials and cutting-edge production techniques. Our rollers are made to endure the rigorous circumstances of ongoing pellet production.
- Options for Customization: We are aware that various applications call for various roller specifications. Orion Engineering Works provides a range of sizes, groove designs, and materials to suit your unique requirements.
- Professional Technical Support: To help you choose the best rollers for your application and maximize your pelleting process, our staff of skilled engineers offers professional technical support and direction. We are always available to respond to your inquiries and offer answers for your problems.
- Competitive Pricing: We provide affordable prices without sacrificing quality. We are committed to giving our clients value by supplying high-quality items at competitive costs.
- On-time Delivery: We recognize how critical it is to reduce downtime. In order to maintain your production, Orion Engineering Works is dedicated to providing your rollers on schedule.
- A wealth of industry experience: Orion Engineering Works has worked in the pelleting business for many years, giving us a thorough understanding of the needs and difficulties faced by our clients. We use our experience to provide dependable and creative solutions.
- Emphasis on Innovation: To enhance our goods and procedures, we are continuously spending money on research and development. In order to provide our clients state-of-the-art solutions, we keep abreast of the most recent developments in pelleting technology.
- Broad Product Offering: We provide more than just rollers. Die sets, shafts, and other necessary parts are among the many pellet mill components offered by Orion Engineering Works. As a result, we can handle all of your pelleting requirements in one place.
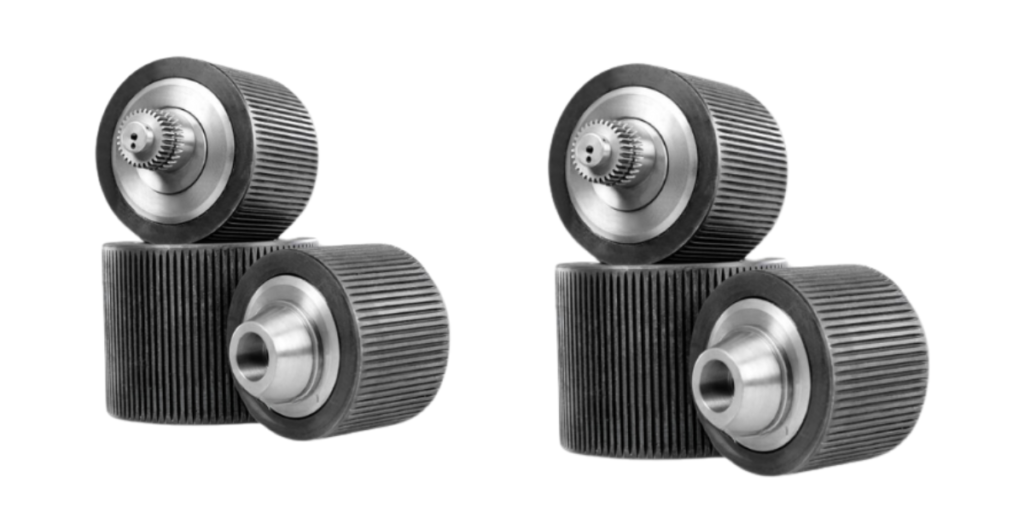
Applications of Pellet Mill Roller
- Material: Hardened steel alloys are commonly used to make rollers. The hardness, durability, and wear resistance of the roller are determined by the particular alloy and heat treatment procedure. Seek out rollers composed of premium materials that are resistant to the abrasive properties of the materials being pelleted.
- Roller Profile: The pelleting process is greatly impacted by the roller surface profile, which includes knurls, corrugations, and grooves. Various profiles are appropriate for various materials and the required properties of the pellet.
- Size and Dimensions: The rollers’ dimensions and size must match those of your particular pellet mill. For best results, make sure the rollers fit correctly and offer the required clearance.
- Manufacturing Quality: Consistent roller performance and longevity depend heavily on the accuracy and caliber of the manufacturing process. Seek out rollers manufactured by reliable companies that adhere to stringent quality control guidelines.
- Heat Treatment: The hardness and durability of the roller are greatly influenced by the heat treatment procedure. The roller’s ability to tolerate the high pressures and temperatures required for pelleting will be guaranteed by a suitable heat treatment procedure.
- Application: The kind of roller you require will be greatly influenced by the kind of material you are pelleting. For instance, different roller profiles are needed for pelleting wood or grains than for pelleting fibrous materials like hay.
- Production of Animal Feed: Pellet mill rollers are necessary to create premium feed pellets for aquaculture, poultry, and cattle. Optimal animal nutrition and growth are guaranteed by consistent pellet quality.
- Production of Biofuel: Wood pellets and other biomass pellets are made using pellet mill rollers and used as renewable energy sources.
- Production of Pet Food: Dry pet food pellets in a range of sizes and shapes are produced using pellet mill rollers.
Types of Pellet Mill Rollers
- Smooth Rollers: These are usually employed for applications requiring a smooth pellet surface and for softer materials.
- Grooved Rollers: Especially for fibrous or slippery materials, grooves improve feeding and compression by increasing the grip on the material. The degree of aggression offered by various groove patterns (axial, spiral, and checkered) varies.
- Dimpled rollers are very helpful for tiny powders or materials that are prone to slipping because they improve the roller’s capacity to grasp and compress the material.
- Segmented Rollers: These rollers have several segments, making it simpler to repair and maintain individual parts.
- Hardened Rollers: These rollers have greater longevity and wear resistance because they are made of high-strength alloys or undergo hardening procedures.
- Smooth Rollers: These rollers are used for materials like soft fibers or fine grains that don’t need to be compressed as much. They are perfect for creating smooth-surfaced pellets.
- Grooved Rollers: These rollers have grooves or serrations on the outside that improve compression and grip. They work well with materials that are harder to compress, such high-density or coarse-fibered materials. Depending on the particular use, the groove pattern may change.
- Corrugated Rollers: These rollers offer a more forceful compression action because of their array of ridges and valleys. They are applied to commodities like biomass or wood chips that need to be compressed heavily.
- Rollers with little indentations or dimples on their surface are known as dimpled rollers. Particularly for slippery or challenging-to-handle materials, these dimples aid in improving the material’s compression and grip.
Benefits of Pellet Mill Roller
- Better Pellet Quality: Our carefully designed rollers provide uniform pellet density, size, and shape, improving the quality of the final product.
- Enhanced Production Capacity: By optimizing throughput, our effective roller designs raise your total production capacity.
- Decreased Operational expenses: By extending machine lifespan and minimizing maintenance, our robust rollers lower operating expenses.
- Enhanced Energy Efficiency: By minimizing energy usage, our effective compression lowers operating expenses and your environmental impact.
- Dependable Performance: Our premium rollers operate smoothly and effectively thanks to their consistent and dependable performance.
- Peace of Mind: Knowing that Orion Engineering Works is a reputable and knowledgeable supplier offers you peace of mind.
- Material Type: The right roller type depends on the kind of raw material being processed, such as grains, biomass, or feed.
- Pellet Size and Density: The roller and die specifications are influenced by the intended pellet size and density.
- manufacturing Capacity: The size and quantity of rollers required are determined by the necessary manufacturing capacity.
- Material and Hardness of the Roller: Hardened steel alloys are commonly used to make rollers. Durability and wear resistance are influenced by hardness and material composition.
- Roller Surface Pattern: The properties of the material should be taken into consideration while selecting a corrugation, dimple, or smooth surface pattern.
Conclusion
The unsung heroes of pellet production, pellet mill rollers are essential to many different sectors in the United States. Optimizing pellet output and increasing profitability requires a thorough understanding of their types, significance, maintenance requirements, and performance-influencing variables.Purchasing premium rollers from reliable vendors such as Orion Engineering Works guarantees greater efficiency, decreased downtime, and constant pellet quality. We are the best Pellet Mill Roller Exporter.
You can guarantee the long-term viability of your pellet production operations by placing a high priority on quality and maintenance.You can rely on Orion Engineering Works to provide outstanding quality, performance, and service for all of your pellet mill roller needs. To find out more about our offerings and how we can support you in reaching your production objectives, get in touch with us right now.